Our philosophy is simple: quality products and extraordinary service — every customer, every time. We want to be true partners with our customers and develop a deep understanding of their businesses so that we can provide proactive solutions that make their lives easier.
The performance of corrugated packaging depends upon factors such as paper quality, production process, box design, handling and the environment. Our design team has extensive experience in developing application specific packaging. By applying engineering principles to calculate the compression strength, puncture resistance and stacking height of our boxes we are able to accurately predict their performance under changing environmental and handling conditions.:
Inward testing: All raw materials are tested before use in manufacturing such as Kraft paper is checked for GSM, Burst Factor, Moisture, COBB-60, & RCT-CD value of paper. We use Euro Glue which is manufactured in house and has high bonding, Fungus Resistance as per the international standards. We use Pining wire which is rust proof and copper / brass for specific clients as per the requirements.
In-line Inspection: Board finish, calliper, flute crush, ECT, BS, Print Uniformity, & adhesive solid content.
Final Inspection: Size, moisture in box, the Bursting strength & Compression strength of box is checked & then duly bundled with proper label mark on bundles, test reports sent along with delivery vehicle.
CORRUGATED BOARD TESTING
Bursting Strength, Bursting Factor, Edge Crush Test, Ring Crush Test, COBB60, Pin Adhesion Test, Box Compression Strength, STFI, Puncture Resistance Test, Tear Factor, Paper Breaking Length, Moisture %, Drop Test, Vibration Test, etc.
According to standards: ISO 2758 / 2759 – SCAN P25/P24 TAPPI T403 / T807 / 810 – PAPTAC D19P/D8 – BS 3137 – DIN 53141 AP / AS 1301.403 – ASTM D47
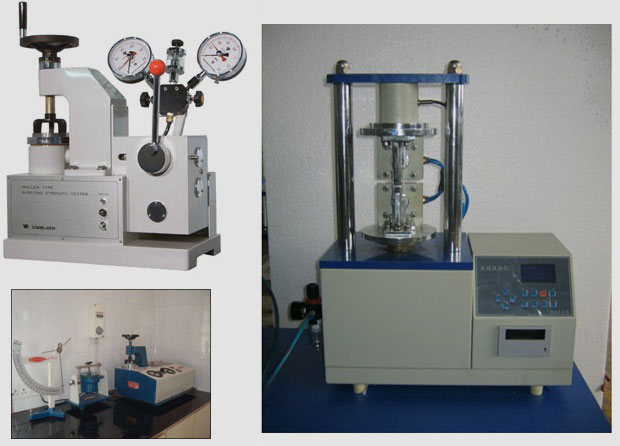
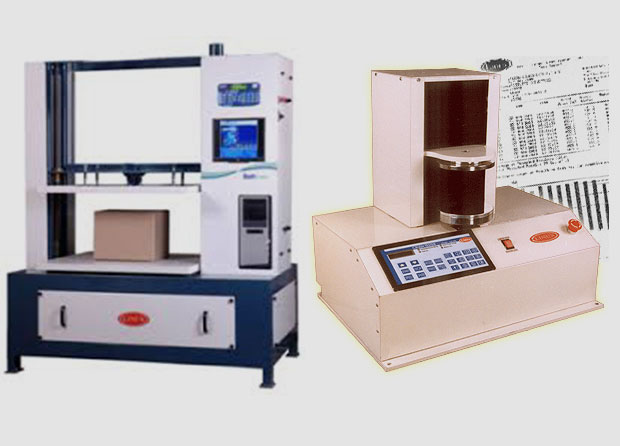
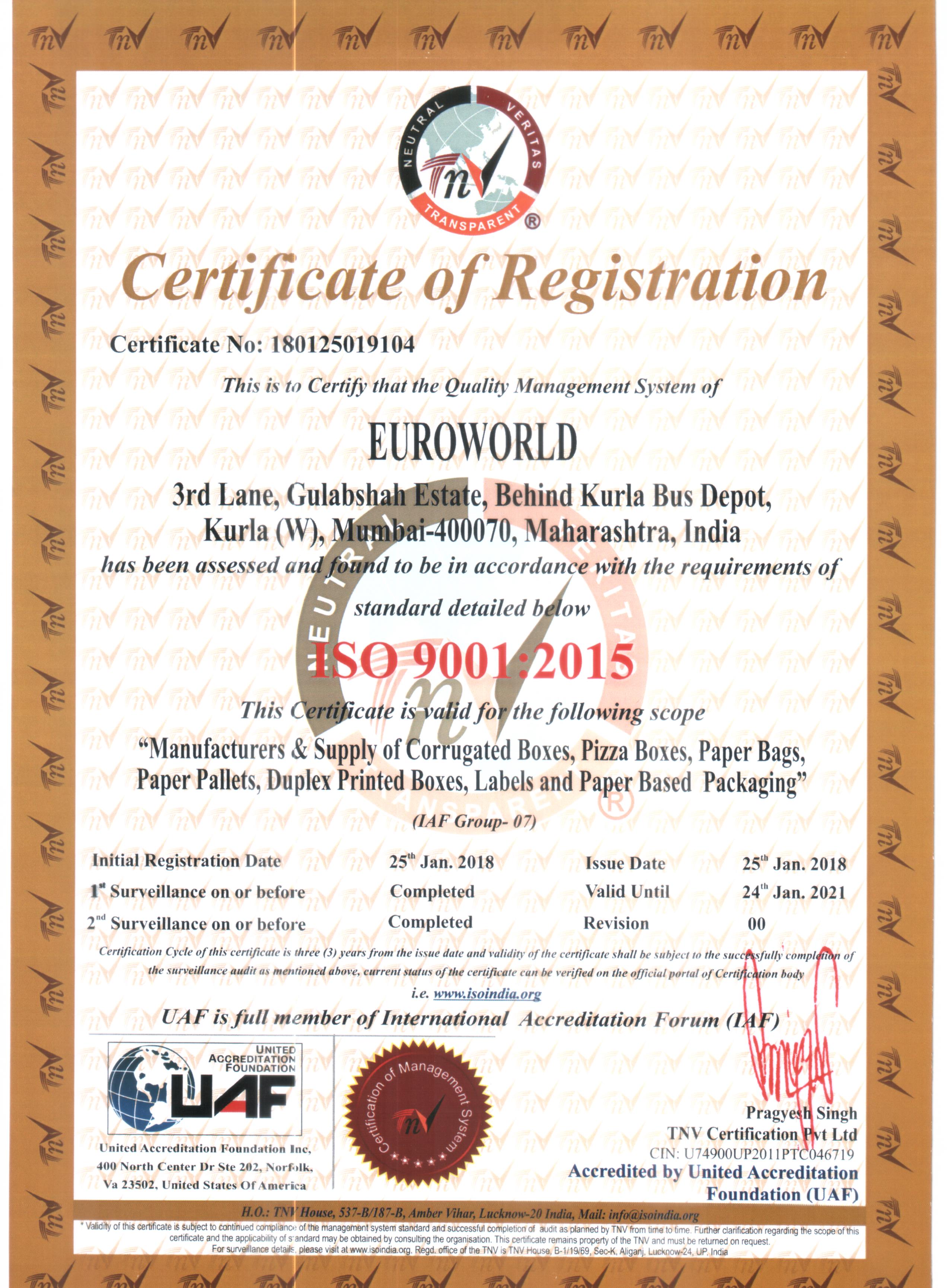
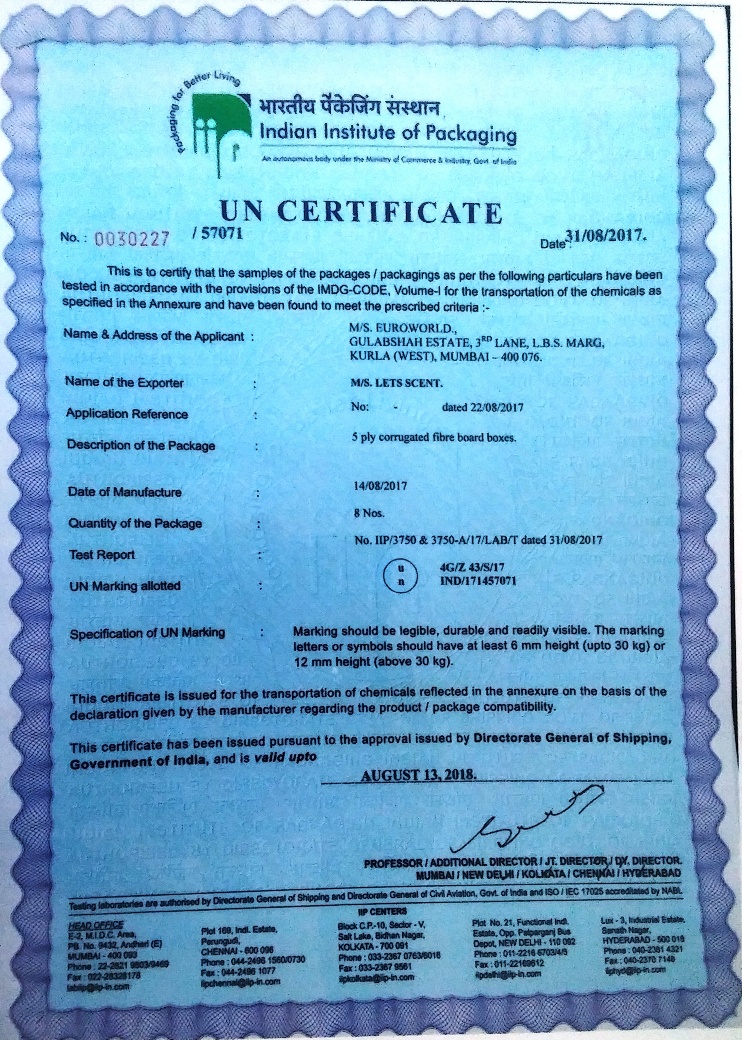
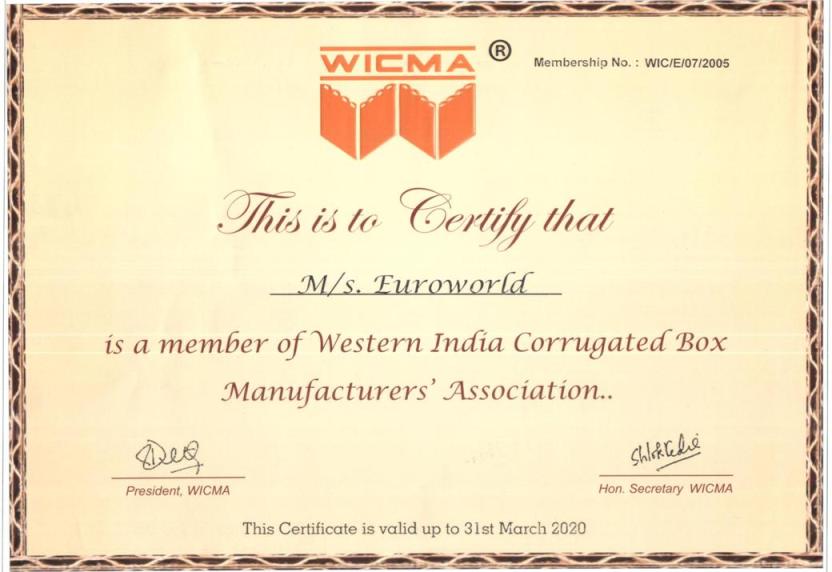